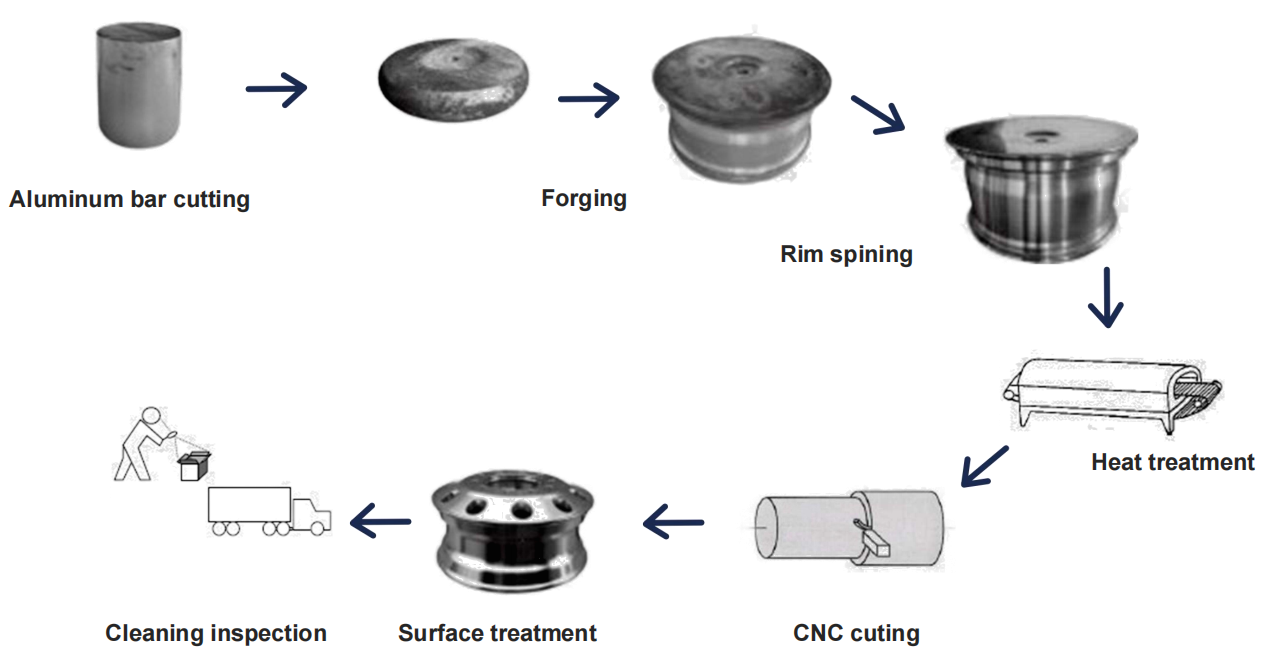
1. ALUMINUM BAR TEST
Each forged aluminum wheels are from one piece of 6061-T6 high-strength aluminum blank. The 6061 aluminum consists of silicon,cooper,manganese,magnesium,zinc,ETC. And after the Homogenizing the wheel will become more denser and stronger
2. CUTTING
Putting the prepared aluminum bar in cutting machine, According to production requirements cutting them into proportionate ingots.
3. PREHEATING
The furnace can control the temperature uniformity and stability and assurance the quality and rate of the heating .Rough forging temperature directly affects the quality of production, using the device can increase the yield of production and reduce production costs.
4. FORGING
After three forging, forging blanks are becoming wheel shape, magnesium alloy becomes more precise, uniform, toughness, can greatly increase the strength and resistance to deformation of the wheel
5. SPINNING TENSILE
Putting the molding forging stock on spinning machine spin-shaped rim, not destroy the material to ensure that the arrangement of the grains, while the spin-out of the rim structure, to achieve the best state.
6. HEAT TREATMENT
Adopting German technology, T6 heat treatment furnace, through twoT4 and T6 heat treatment steps are to strengthen the dealing and is completed after spinning to make forged aluminum wheels overall mechanical strength of the largest and most stable state.
7. PUNCHING
After the heat treatment of the blank into the CNC automatic lathe cutting, cutting out the various wheel disc faces bits and the R angle as per request. Precision CNC lathe machining, to ensure that each wheel has a high-precision roundness and balance, which greatly reduces the wheel deviation, swing and other issues.
8. POLISHING
Adopting the automatic CNC polishing machine imported from Spain will receive the best surface
result without corrosion problems.
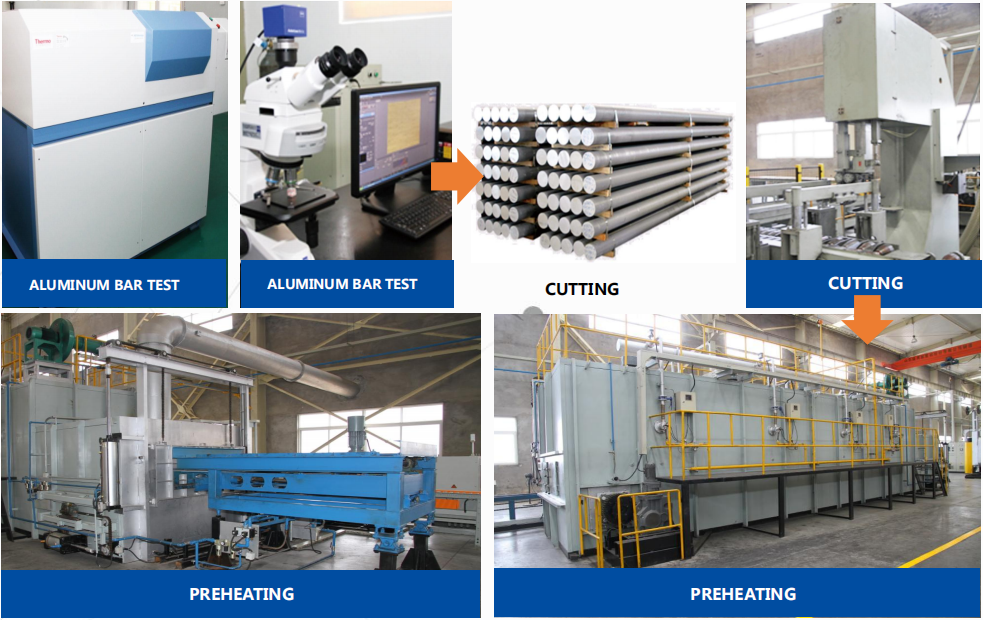
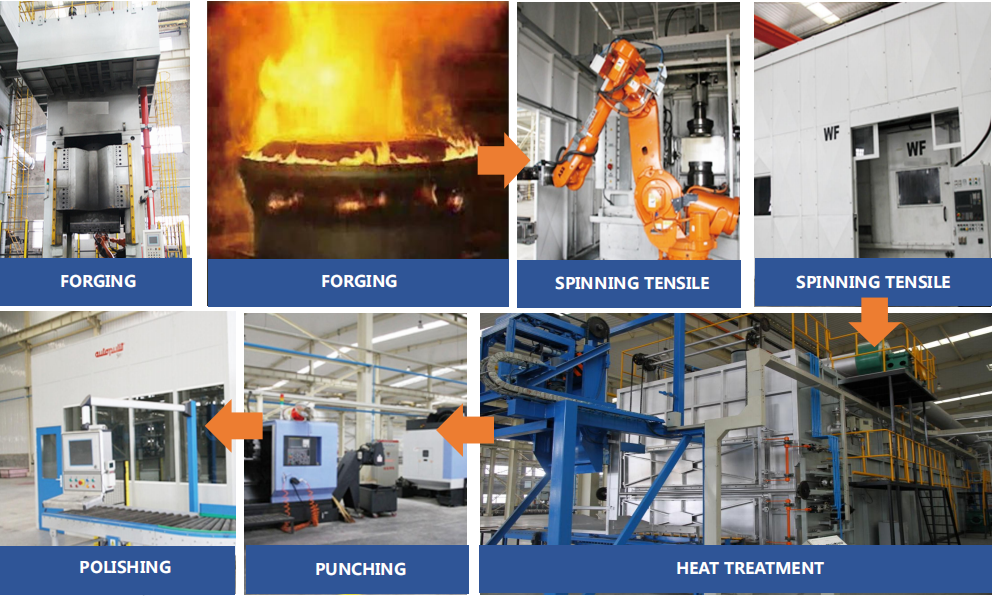
All forged alloy wheels will be tested strictly in the factory to ensure delivery to the customer every forged aluminum wheels achieving optimal product quality